The Customer
This customer operates in the United States, Europe, and Africa. They are an independent global energy company focused on unconventional resource utilization.
Refrigeration Systems — A Key Industry Requirement
Natural gas processing facilities, refineries, petrochemical plants, and integrated chemical complexes rely on large-scale refrigeration systems for the smooth and safe running of their day-to-day operations.
Meeting New Standards
A new and more stringent European regulatory framework on the use of fluorinated greenhouse gases (F gases), such as hydrofluorocarbons (HFCs), has driven the need for a wide range of industrial firms to reappraise the existing stable of aging refrigeration systems. It has also created a fresh opportunity to review and update refrigeration technologies that are no longer delivering maximum efficiencies.
Choosing the Right Refrigerant
This project called for a refrigeration system based on the use of a compliant, non-flammable refrigerant, with a Global Warming Potential (GWP) lower than 2500. As the type of refrigerant has a direct effect on the frequency of the mandatory periodic checks, the choice of the right refrigerant is particularly vital for offshore installations, where there are greater constraints for maintenance and repair operations. Clauger-Technofrigo’s engineers selected a pure, chlorine-free refrigerant, with an ozone depletion potential (ODP) of zero.
Offshore Factors
The project’s offshore context meant Clauger-Technofrigo had to deal with space constraints the existing module occupied a very limited amount of space, so PGE Team had to design around this constraint, as well as weight considerations, to allow lifting and installation activities. Additional factors including transportation logistics, vibration control, and ambient factors were considered. The mechanical design of the proposed solution was supported and explained to the customer using 3D modeling software.
The design includes the use of a double mechanical seal on the compressor to reduce leakages to the atmosphere, and double block and bleed isolation valves in the pressurized lines where a potential repair would occur.
As the offshore application may imply many difficulties related to supplying spare parts and components, especially during the harsh winter season when helicopters and ships face navigational challenges, the operator requested an accurate and deep study on the reliability, availability, and maintainability (RAM) and failure mode, effect and criticality analysis (FMECA) of the plant as a basis for the selection of the appropriate spare parts, for both two years of operation and for capital spare parts. As a result of this study, a complete spare parts list suitable for the specific application, as well as awareness of a broader set of spare parts, was supplied. The results from this study show that the availability of the refrigeration package exceeds 99%.
The String Test
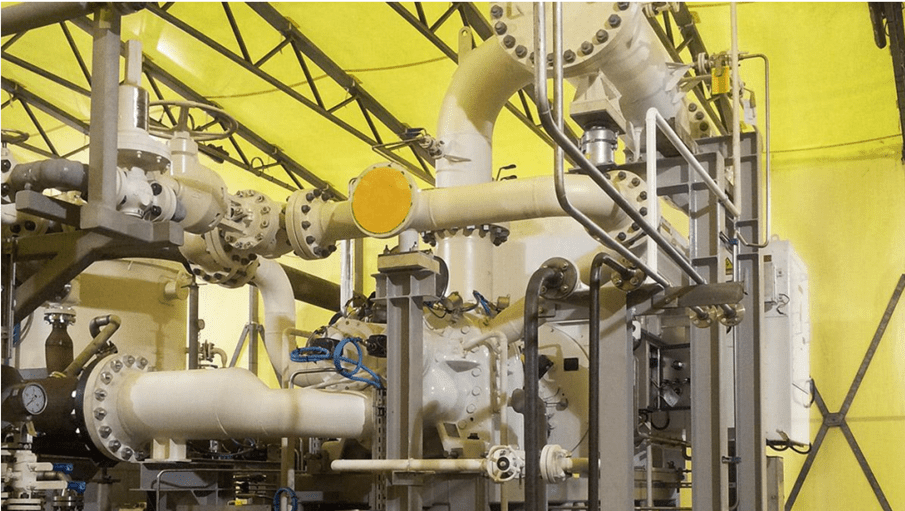
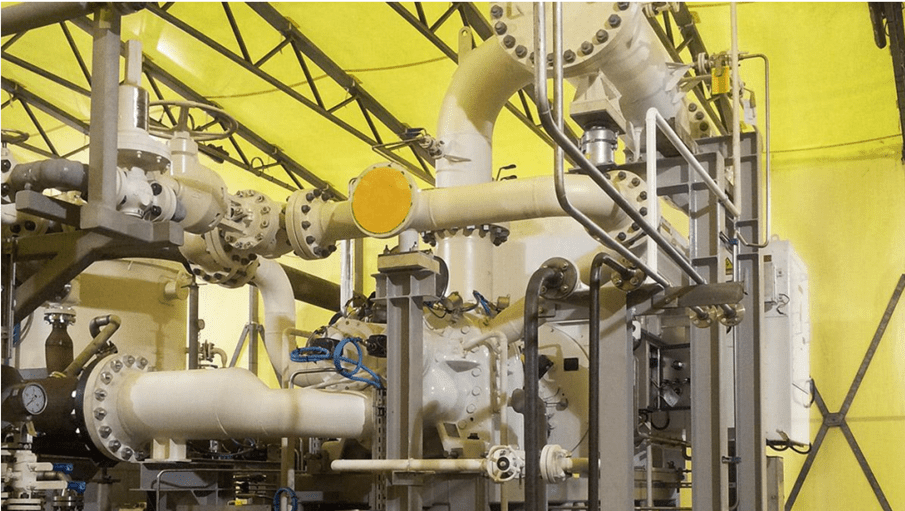
As a final check, the operator requested a complete string test. The test was performed at a workshop before shipment. A complete test was conducted with the project-specific compressor, motor, and lube oil circuit. The facility was equipped with the required test bench suitable for the compressor motor power and for the provision of the utilities needed for the test (cooling water, electricity, nitrogen, air).
Testing of the unit comprised four hours of continuous operation at design speed. This ensures the mechanical integrity of the unit and system functionality. During the test, the noise and vibration levels were monitored.
Our Innovative Solution
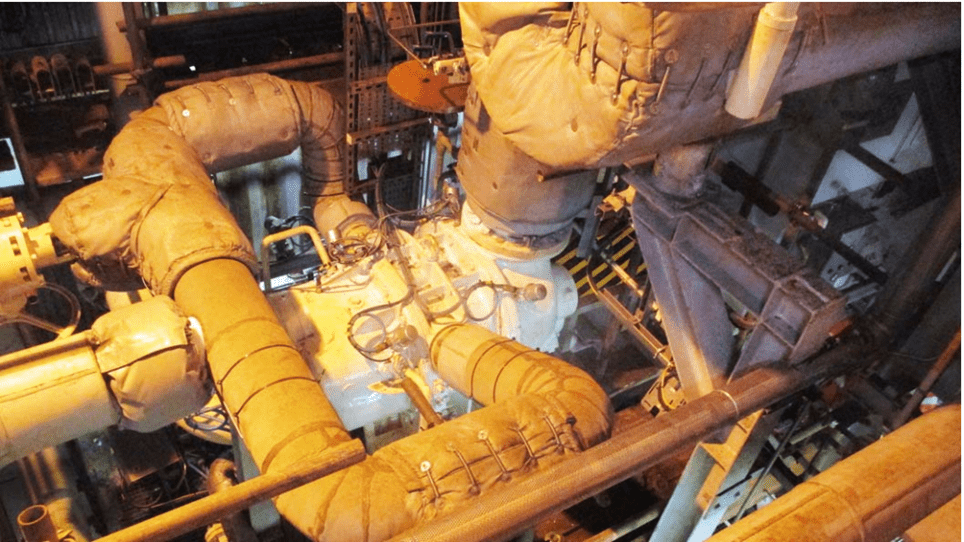
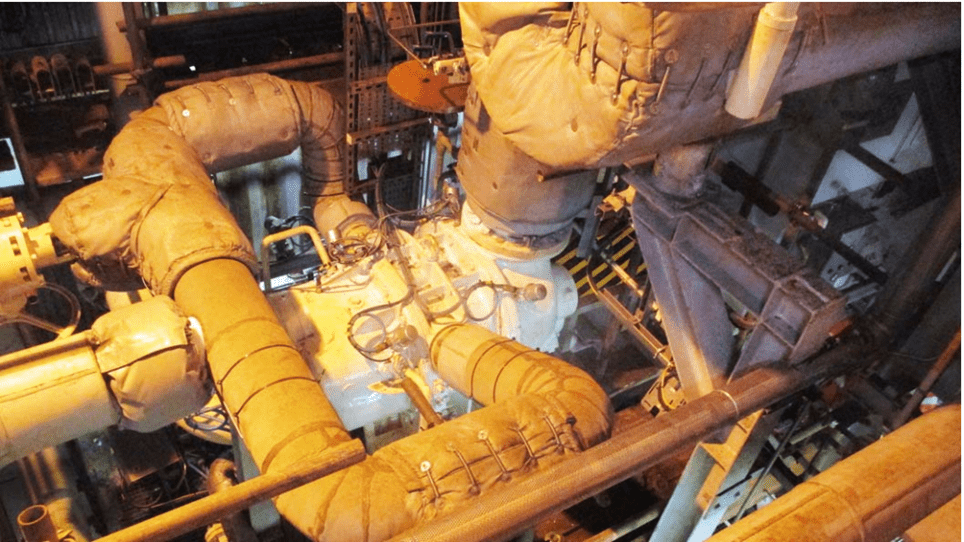
A new refrigeration system was designed around exacting customer specifications, including dehydration & dew point control. PGE team replaced the existing centrifugal compressor technology with an oil-flooded screw compressor and a flooded evaporator — a relatively new application for the flooded technology. Relative to an equivalent-duty centrifugal compressor, opting for a rotary screw compressor delivered lower installation costs to the customer. In addition, it offered smaller physical dimensions and greater ease of maintenance, due to the durability of the mechanical seal. The typical maintenance period for an oil-flooded screw is three years. This extended mandatory maintenance interval ensures high availability of the system.
Thanks to PGE’s forward-thinking process systems team — which expanded the range of technical possibilities to find a highly reliable, low-maintenance solution for the customer — a successful outcome was achieved.
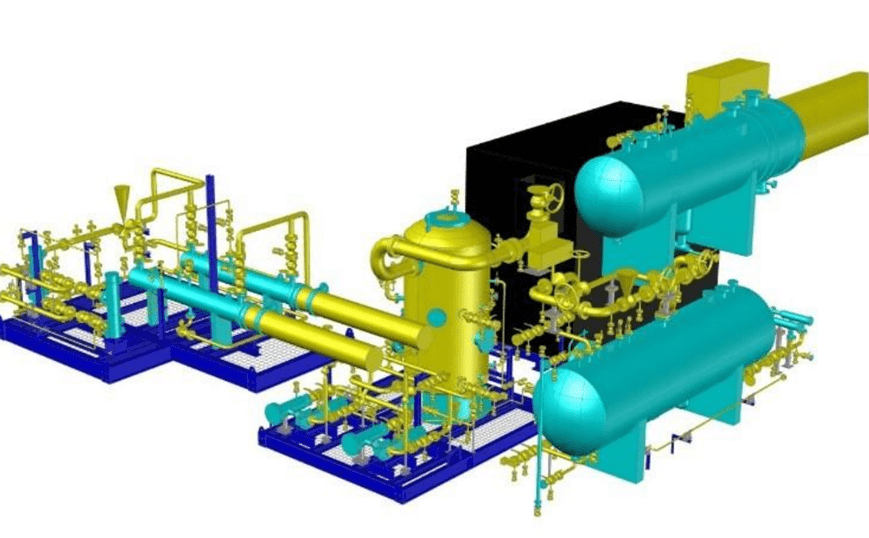
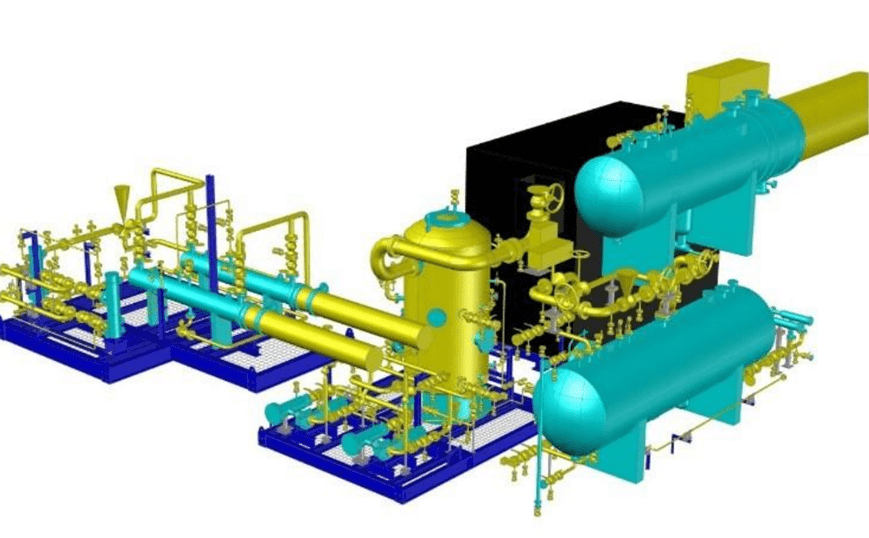